- Feb 24, 2025
- News
What is a Gantry Crane Girder?
A gantry crane girder is a horizontal beam that supports the hoist of a gantry crane. Gantry cranes can have either a single or double girder configuration.
Have you ever walked into a massive factory or strolled past a busy shipping yard and noticed those giant structures lifting and moving heavy stuff around like it's no big deal? Chances are, you've seen a gantry crane in action. An important part of the crane for lifting objects is the lifting beam. But what exactly is it, and why does it matter? In this article, we're going to break it all down—what a gantry crane girder is, how it works, and why it's such a game-changer for industries that deal with heavy equipment and materials. Let's dive in!
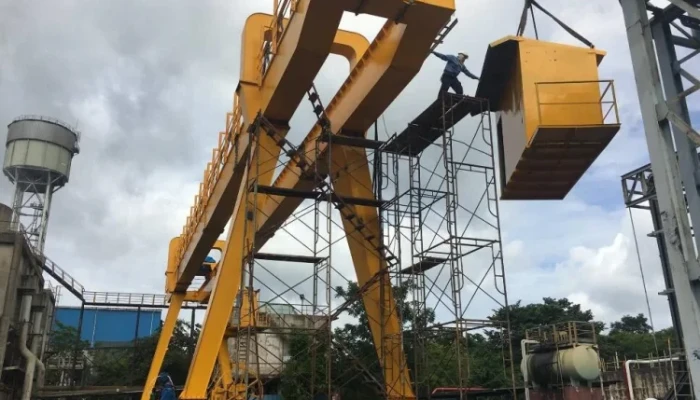
What's a Gantry Crane, Anyway?
Before we get into the nitty-gritty of the gantry girder, let's start with the basics. A gantry crane is a type of overhead crane that's built to lift and move heavy loads. It's got legs that run along a fixed track or rail, which lets it travel across a workspace. You'll spot these cranes in places like construction sites, warehouses, manufacturing plants, and shipping ports. They're the heavy lifters of the industrial world, capable of handling anything from steel beams to massive shipping containers.
Gantry cranes come in all shapes and sizes. Some are small and portable, perfect for tighter spaces, while others are towering giants that can hoist hundreds of tons. What makes them so handy is their ability to work both indoors and outdoors, adapting to whatever job's at hand.
What's the Gantry Crane Girder?
Now that we've got the crane part covered, let's zoom in on the gantry crane girder. Picture it as the backbone of the whole operation. The gantry girder is the horizontal beam that stretches across the width of the crane. It's what holds up the hoist and trolley—the parts that actually do the lifting and moving. Without the girder, the crane wouldn't have the strength or stability to handle those hefty loads.
Typically made of steel, the gantry girder is built tough to support not just the weight of whatever's being lifted but also the forces that come with moving it around.
Gantry girders come in two main flavors: single girder and double girder. A single girder crane has just one beam, which works fine for lighter loads. Double girder cranes, with two beams, are beefier and better suited for heavier-duty tasks. The choice depends on what you're lifting and how much muscle you need.
Types of Gantry Girders
Just like there are different types of gantry cranes (full gantry, semi-gantry, portable gantry, etc.), there are also different types of gantry crane girders, each with its own characteristics and best-suited applications.
1. Box Girder
This one's shaped like a hollow box, which gives it a lot of strength and stiffness. It's the go-to choice for heavy-duty jobs where you're lifting big loads over wide spans. This construction has the following characteristics:
- Superior Strength-to-Weight Ratio: The enclosed box shape provides exceptional strength and torsional stiffness for its weight. This means box girders can handle very heavy loads and resist twisting forces effectively, even over long spans.
- High Torsional Rigidity: The closed box section is inherently resistant to twisting or torsion, which is crucial for maintaining stability and preventing load sway, especially with off-center loads.
- Clean and Enclosed Design: The box shape is relatively clean and enclosed, which can offer some protection to internal components and reduce dust and debris accumulation inside the girder.
- Ideal for Heavy Loads and Long Spans: Box girders are the go-to choice for heavy industrial cranes, shipyards, container handling gantry cranes, and applications where very heavy loads are the norm and long spans are required to cover large areas.
2. I-Beam Girder
Also called a wide flange beam, this girder has an I-shaped or H-shaped cross-section. It's lighter than the box girder, making it a good pick for smaller cranes or spaces where you don't need as much heft. This type of beam has the following characteristics:
- Simple manufacturing: Plate girders are generally simpler and more economical to fabricate than box girders, especially for shorter spans and lighter to medium-duty applications. The fabrication process is more straightforward, often involving less welding and machining.
- Moderate intensity: Although the plate girder is not as torsionally stiff as the box girder, it has a structure with high flexural and shear stiffness. This strength is sufficient for many common crane applications.
- Versatile Design Options: Plate girders can be easily customized in terms of plate thickness, web height, and flange width to optimize the girder design for specific load and span requirements.
- Suitable for Medium to Heavy Loads and Moderate Spans: Plate girders are commonly used in manufacturing facilities, warehouses, fabrication shops, and general industrial applications where loads are not excessively heavy and spans are moderate.
3. Truss Girder
Made up of triangular units, the truss girder is all about keeping things light without sacrificing strength. It's often used when the crane needs to cover a long distance, like in a sprawling warehouse or shipyard.
- Truss Girders: Although less common in common industrial applications, truss beams are due to their unique design that makes them more suitable for outdoor applications, such as in windy or gusty areas, where they are constructed to be highly wind resistant. However, they can be more complex to manufacture and may require more maintenance.
- Lattice Girders: Similar to truss girders, lattice girders are also lightweight and strong, constructed from interconnected members forming a lattice pattern. Like truss girders, they are less common for typical industrial gantry crane girders but might find niche applications.
4. Lattice Girders
Similar to truss girders, lattice girders are also lightweight and strong, constructed from interconnected members forming a lattice pattern. Like truss girders, they are less common for typical industrial gantry crane girders but might find niche applications.
For most industrial gantry crane applications, especially those requiring robust performance and handling heavy loads, box girders and plate girders are the dominant and most practical choices.
Materials and Construction
The gantry crane girder material is almost always steel. Steel is chosen for its exceptional strength, stiffness, weldability, and cost-effectiveness. The specific type of steel used will depend on the crane's capacity, operating environment, and design requirements, but common grades include:
- Structural Steel (e.g., ASTM A36, A572): These are common carbon steels widely used in structural applications, offering a good balance of strength and weldability.
- High-Strength Low-Alloy (HSLA) Steel: HSLA steels offer higher strength than standard structural steels, allowing for lighter girder designs without sacrificing load-bearing capacity. Examples include A572 Grade 50 or similar grades.
- Weathering Steel (e.g., Corten Steel): In outdoor applications where corrosion resistance is a concern, weathering steel can be used. It forms a protective rust layer over time, reducing the need for painting and maintenance.
Gantry girder fabrication typically involves these key processes:
- Cutting Steel Plates: Steel plates are precisely cut to the required shapes and sizes using CNC cutting machines, lasers, or plasma cutters.
- Welding: For both box and plate girders, welding is the primary method of joining steel plates together to form the girder section. High-quality welding procedures and qualified welders are essential to ensure strong and reliable welds. Welding techniques like submerged arc welding (SAW) or flux-cored arc welding (FCAW) are often used for their efficiency and weld quality.
- Stiffening and Bracing: Depending on the girder type and design, stiffeners and bracing elements are welded inside box girders or to plate girders to enhance stiffness, prevent buckling, and improve load distribution.
- Machining and Finishing: After welding, the girder may undergo machining processes to ensure precise dimensions and smooth surfaces, especially for the trolley runway. Surface finishing, such as painting or coating, is applied for corrosion protection and aesthetics.
- Inspection and Testing: Throughout the fabrication process, and especially after welding, rigorous inspections and non-destructive testing (NDT) methods (like ultrasonic testing or magnetic particle testing) are used to verify weld quality, structural integrity, and dimensional accuracy of the girder.
Design Considerations
Gantry girder design is a complex engineering process that takes into account numerous factors to ensure the girder is safe, efficient, and meets the specific operational requirements of the crane. Key design considerations include:
- Load Capacity: The maximum load the crane is designed to lift is the primary driver of girder design. Heavier loads necessitate stronger and more robust girder sections.
- Span Length: The distance between the crane legs (the span) directly affects the bending moments and stresses in the girder. Longer spans require deeper and heavier girders to maintain stiffness and prevent excessive deflection.
- Deflection Limits: Allowable deflection (bending) of the girder under load is strictly controlled to ensure proper crane operation and prevent excessive load sway or instability. Industry standards and codes specify maximum permissible deflection limits.
- Duty Cycle and Fatigue: The crane's duty cycle (how frequently and intensely it is used) and anticipated fatigue life are considered in the design. Cranes used for heavy, continuous operation require girders designed for high fatigue resistance.
- Environmental Conditions: Operating environment factors like wind loads, temperature extremes, and corrosive atmospheres are taken into account in the girder design and material selection. Outdoor cranes, for example, must be designed to withstand wind forces and weather exposure.
- Safety Factors: Structural design codes mandate specific safety factors that must be applied to stress calculations to ensure the girder can safely handle unexpected loads and operating conditions.
- Fabrication and Erection Considerations: The girder design should also consider how it will be fabricated, transported, and erected on-site. Segmented girder designs may be used for very long spans to facilitate transportation and assembly.
- Compliance with Standards and Codes: Gantry girder design must comply with relevant industry standards and codes, such as those from the American Institute of Steel Construction (AISC), the Crane Manufacturers Association of America (CMAA), or international standards like ISO or EN crane standards.
Conclusion
A gantry crane beam may look like a simple metal beam, but there are many factors to consider when designing or selecting one. It supports heavy materials and is an essential and vital part of crane operation.