- Nov 13, 2024
- News
Overhead Crane Inspection Checklist
Overhead crane inspection checklists typically include control mechanisms, structural components, hooks, safety devices, wire ropes, electrical components and more.
Overhead cranes are an important piece of equipment in the workshops of various industrial industries, providing an efficient way of lifting and transporting heavy loads in the workshop. In case of equipment downtime, it will bring losses to the whole production line or workshop work. Therefore, to ensure their safe and optimal operation, regular inspections are essential. These inspections help identify potential issues before they escalate, ensuring safety and compliance with regulations. This article provides a comprehensive overview of the overhead crane inspection checklist, discussing key components, inspection frequencies, and some measures.
Why is Overhead Crane Inspection Important?
Regular inspections of overhead cranes are mandated by regulatory bodies, including the Occupational Safety and Health Administration (OSHA) in the United States and specific state regulations like WAC 296-24-23519. Inspections are designed to:
- Identify wear and tear or potential hazards.
- Maintain safe operational standards.
- Comply with legal requirements to prevent liability issues.
- Ensure reliability and minimize equipment downtime.
An effective overhead crane inspection checklist allows operators to systematically assess and document the crane's condition, promoting a safe working environment.
Types of Inspections
Overhead crane inspections fall into two main categories: frequent and periodic.
Frequent Inspections
Frequent inspections are conducted before each use or daily, focusing on the crane's essential components. This type of inspection should also be completed monthly for cranes that are in regular use. Frequent inspections are generally visual and performed by the crane operator or another qualified individual.
Key items for frequent inspections include:
- Controls and Operating Mechanisms: Ensure buttons, levers, and other controls function properly without sticking or unusual wear.
- Hooks: Check for cracks, bending, or twisting. The hook's throat opening should not exceed a certain threshold (typically 15% more than the nominal opening), and the tip should not twist more than 10° from its original plane.
- Safety Devices: Safety guards, interlocks, and any protective barriers should be in place and functioning correctly.
- Load Chain and Wire Rope: Check for signs of wear, such as broken wires, flat spots, or signs of elongation beyond manufacturer specifications.
- Electrical Components: Inspect for exposed wires, loose connections, and proper enclosure.
Periodic Inspections
Periodic inspections are more thorough and occur at longer intervals, typically every 6 to 12 months. These inspections require a certified inspector and may involve disassembly and more detailed examination of internal components.
Periodic inspection items include:
- Structural Components: Inspect for deformation, rust, cracks, or any sign of structural fatigue in beams, sheaves, and drums.
- Mechanical and Hydraulic Systems: Ensure proper operation of brakes, gears, bearings, and rollers.
- Motor and Electrical Systems: Evaluate the condition of wiring, motors, and brake mechanisms.
- Load Handling Equipment: Assess the condition of slings, hooks, and lifting devices. These items should meet all manufacturer and regulatory standards.
Detailed Checklist for Overhead Crane Inspections
Below is a comprehensive checklist covering frequent and periodic inspection requirements. This checklist is designed to guide inspectors in evaluating the crane's condition and identifying any necessary repairs.
Inspection Item | Frequent (Daily/Monthly) | Periodic (6-12 Months) | Inspection Focus |
---|---|---|---|
Controls & Operating Mechanisms | ✔ | ✔ | Ensure controls operate smoothly, without sticking, and return to the off position. |
Hooks | ✔ | ✔ | Check for cracks, wear, excessive throat opening, or tip twisting. Latch should function properly. |
Load Chain & Wire Rope | ✔ | ✔ | Inspect for broken wires, wear, or elongation. Verify lubrication and check for rust or corrosion. |
Safety Devices | ✔ | ✔ | Check interlocks, guards, and any other protective devices for proper functionality. |
Outriggers & Foundation | - | ✔ | Assess stability and condition of outriggers, foundation, and cribbing. |
Motor & Brake System | ✔ (brake test) | ✔ | Test motor brakes for correct operation, ensuring no drift occurs after releasing control. |
Electrical Components | ✔ | ✔ | Look for exposed wiring, loose connections, and deterioration of insulation. |
Structural Integrity | - | ✔ | Inspect beams, welds, and joints for signs of cracking, rust, or deformation. |
Fire Extinguisher | ✔ | ✔ | Ensure fire extinguisher is accessible and fully charged on cab-operated cranes. |
Limit Switches | ✔ | ✔ | Test upper and lower limit switches under no-load conditions. |
Labels & Indicators | ✔ | ✔ | Verify visibility and accuracy of load indicators, wind indicators, and warning labels. |
Drive Mechanisms | - | ✔ | Inspect drive gears, bearings, and shafts for wear, lubrication, and alignment. |
Note: A more detailed list tailored to each crane's specific configuration and manufacturer recommendations is advisable for accurate inspection records.
Inspection Best Practices
Documentation and Record-Keeping
Accurate records are essential for maintaining crane safety and regulatory compliance. According to OSHA and other regulatory bodies, records of frequent inspections should be retained for at least one year. For periodic inspections, a detailed log including any repairs or replacements should be maintained.
Tagging Out Defective Equipment
If any deficiencies are identified during an inspection, the crane should be tagged as "out of service" until repairs are made. This is especially important for critical components like load-bearing parts, brakes, or safety mechanisms. Operators should refrain from using the crane until it has been certified safe for operation.
Pre-Operation Testing
Before each shift, operators should perform a quick functional test of key components, such as the control buttons, warning alarms, and limit switches. Testing ensures the crane's essential functions are ready for use.
Preventive Maintenance
Routine preventive maintenance according to the manufacturer's recommendations can prevent unexpected equipment failures. Maintenance tasks should include lubrication, tightening of bolts, checking fluid levels, and replacing worn components.
Key Compliance Standards
Several standards govern overhead crane inspections, including:
- OSHA 1910.179: Outlines the inspection frequency, requirements, and record-keeping procedures for overhead cranes.
- ASME B30.2: Provides guidelines for the construction and safe operation of overhead and gantry cranes.
- ANSI/ASME Standards: Offers additional safety protocols for handling loads, emergency stops, and more.
Adhering to these standards not only ensures safety but also minimizes liability and operational risks. Compliance with industry standards protects workers, reduces downtime, and ensures operational efficiency.
Conclusion
Regular inspections of overhead cranes are critical to the safe and efficient operation of lifting and transportation projects. Following a comprehensive inspection checklist ensures that all critical components are evaluated for wear, damage, and proper function. This approach to crane safety not only aligns with OSHA and ANSI requirements but also fosters a proactive safety culture. Properly documented inspections, preventive maintenance, and immediate repairs of detected issues will maximize crane performance and contribute to a safe and efficient work environment.
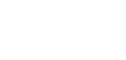
Yuantai Crane
Yuantai, with a decade of crane manufacturing expertise in Changyuan, Henan, operates a facility spanning 240,000 square meters, producing over 10,000 sets annually valued at RMB 1.5 billion. They export top-quality European-style cranes to 150+ countries, serving diverse industries such as steel and petrochemicals.
Contact to Get Solution & Price
Respond quickly to customer needs, questions and create value.