- May 14, 2025
- Case Studies
10t LD Model Traditional Bridge Crane With MD Hoist
Discover the 10t LD Model Traditional Bridge Crane equipped with an MD Hoist, designed for optimal efficiency in machinery manufacturing plants. Enhance your operations today.
A machinery manufacturing plant recently upgraded its lifting equipment to handle heavier loads in a compact workshop. Overhead cranes are critical in manufacturing for lifting large parts safely and efficiently. In this crane installation case study, we examine how a Yuantai LD model single-girder overhead bridge crane with an MD electric hoist met the customer's needs. The upgrade addressed the plant's space constraints and increased load requirements, resulting in faster assembly and improved safety.
Customer Background and Requirements


The customer is a machinery manufacturer that assembles large machine frames, molds, and sub-assemblies. Their existing overhead lifting system was limited to 5 tons, which proved inadequate for newer, heavier components. Key requirements emerged:
- Load Capacity: Handle up to 10 tons, doubling the previous limit.
- Span and Lifting Height: Cover a 9m span across the workspace with 6m lifting height.
- Building Height Constraint: Shop ceilings were low, so the crane needed a low headroom design.
- Controls: Include both pendant and remote radio control for operator flexibility.
- Electrical Supply: Operate on the factory's 380V/50Hz three-phase power.
- Duty Class: Rated A3 (FEM 1Am) for moderate, continuous usage, typical of assembly work.
Before the new crane, heavy parts often required manual handling or forklift transfers. This led to production delays and safety risks. OSHA and industry guidelines stress that mechanized lifting is essential to prevent injuries and inefficiencies in heavy manufacturing. The facility needed a compact overhead lifting solution that fit the building height while lifting 10t loads reliably.
Challenges and Constraints
The main challenges were the load increase and spatial restrictions in the shop. The existing crane system could not lift parts heavier than 5 tons, causing operators to improvise with manual hoists or jacks. This slow, labor-intensive process not only delayed assembly but exposed workers to injury risks from lifting heavy items.
Space was another constraint. The shop roof height did not allow a large double-girder crane or tall end-trucks. Installing a high-profile crane would have reduced floor clearance and potentially interfered with other equipment. In such low-headroom environments, a specialized design is needed.
Given these factors, the customer sought an LD model single-girder overhead crane with a low-profile MD hoist. This setup could provide the required 10t capacity while keeping the lifting machinery low enough to fit the building. The solution would replace delay-prone manual methods with a safe, efficient overhead lifting system.
Yuantai 10t LD Single-Girder Crane with MD Electric Hoist
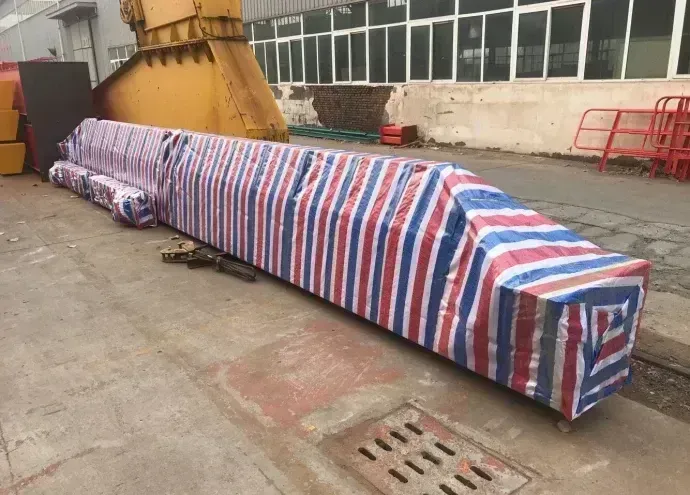
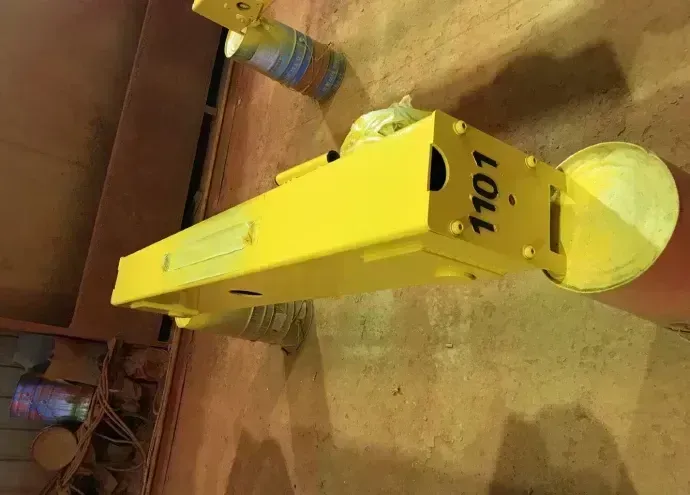
Yuantai Crane offered a 10t LD single-girder bridge crane with an MD electric wire rope hoist. The LD series is a conventional Chinese design for single-girder EOT (electric overhead traveling) cranes. It is known for mature technology, simple structure, and long service life, making it cost-effective for light to moderate-duty use. And cranes in this configuration are much less expensive and cost little compared to other models. The MD hoist is a dual-speed electric wire rope hoist that can switch between normal and low lifting speeds, allowing precise load positioning. The key reasons for this choice include:
- Low Headroom Design: The LD single girder requires less vertical space than double-girder cranes, preserving floor clearance. The MD hoist also has a compact design to maximize lifting height in a limited bay.
- Capacity and Span Fit Requirements: The crane was custom-built for 10t capacity, 9m span, and 6m lift height. The LD series can cover spans from about 3m up to 31.5m and lifting heights up to 18m.
- Duty Class: The system meets an A3 duty rating (FEM 1Am) for moderate use. A FEM 1Am (ISO M4) class is intended for light-to-medium duty cycle, matching the workshop's usage. In fact, the MD1 hoist is rated for A3/A4 duty and provides the specified dual-speed feature.
- Cost and Simplicity: Single-girder designs are generally less expensive and easier to install than double-girder cranes. The customer needed a cost-effective, adaptable solution for moderate-duty lifting (as opposed to a heavy-duty crane).
- Flexibility: The LD crane design can accommodate various span lengths and controls. Yuantai's LD cranes typically use either a QS trinity-drive system or a traditional motor+reducer for trolley travel, giving flexibility in configuration.
The customer selected Yuantai's LD model traditional bridge crane (single girder) equipped with an MD electric wire rope hoist. This overhead crane solution could lift heavier parts, fit under the low ceiling, and integrate easily into the existing power and control setup.
Product Requirements
The crane was engineered to meet these specific criteria:
- Capacity: 10tons (10t overhead crane)
- Span: 9meters (coverage across workshop)
- Lifting Height: 6meters maximum hook travel
- Power Supply: 380V, 50Hz, 3-phase (standard industrial power)
- Controls: Pendant control station and wireless remote for operator safety
- Duty Class: A3 (FEM 1Am) – suitable for frequent, moderate lifts
- Headroom: Low-profile design to fit limited building height
These specs ensured the crane could handle the heaviest planned loads without exceeding safety limits, while remaining within the shop's dimensional constraints.
Crane Features and Design
1. Structural Design
The LD crane's main beam is a welded U-shaped steel box-beam (usually Q235B carbon steel) that balances strength with low weight. The end girders are made of rectangular welded steel tubes (Q235B or optional Q345B). This box-beam and welded construction yields a rigid structure that is also relatively light. The total dead weight of the crane is small, which helps reduce track loading. Specialized crane wheels are used on the single girder; these are “light and strong” for smooth travel and good load distribution.
2. MD Electric Wire Rope Hoist
The chosen hoist is an MD-model wire rope hoist rated for 10t. MD hoists are a classic design for single girder cranes. They offer two lifting speeds: a normal speed for quick raising/lowering and a low speed for precise positioning. At low speed, the hoist allows careful placement of heavy workpieces, essential during assembly. The hoist is equipped with a heavy-duty steel wire rope and grooved drum, ensuring smooth layering of rope and long service life. In practice, this MD hoist meets A3 duty (light-medium service) and is more versatile than a single-speed CD hoist for assembly tasks.
3. Safety Devices
The crane includes multiple safety features. Overload protection limits ensure the hoist will not lift beyond its rated 10t. Upper and lower limit switches (hoist limit switches) prevent the hook block from over-traveling into the hoist or trolley frame. End-travel limit switches on the bridge stop the crane at the rail ends, preventing collisions. Anti-collision bumpers are installed on the end trucks. An independent overload limiter signals if a load is too heavy. Such devices are standard on LD cranes. These measures protect the machine and operators, reducing downtime.
4. Electrical and Control
The crane's electrical equipment is separated into two enclosures: one for the bridge/travel mechanism and one for the hoist (lifting) mechanism. This helps isolate electrical components for easier maintenance. Indoor-rated enclosures (e.g. NEMA 12) are dust-tight, protecting the controls and motors from debris. Power is supplied via festooned cables for the hoist trolley and a conductor bar (sliding rail) for bridge travel, ensuring smooth power delivery. Operators control the crane with a handheld pendant or an optional wireless remote transmitter, allowing them to stand clear of moving loads. Pendant controls and remote radio controls are common safety features that let operators maintain a safe distance and visibility while running the crane.
5. Maintenance
The LD crane's simple construction also means straightforward maintenance. Critical wear parts like wheel bearings are lubricated via accessible oil plugs and grease points. Because the main beam is welded steel, it has no large rivets or flanges, reducing inspection points. Users are instructed to regularly check bolt connections and the condition of wheels and brakes. In this case, proper maintenance procedures were communicated to the customer upon handover.
Installation and Commissioning
The crane was manufactured to the specified dimensions and shipped to the customer on schedule. Installation involved mounting the end trucks on the existing runway rails and securing the main beam across the span. Installers tested the bridge travel and trolley motions, confirming alignment and smooth movement before hoist mounting. The MD hoist was attached under the beam and loaded onto the trolley.
During commissioning, the team ran the crane through no-load trials, adjusting limit switches and brakes as needed (this matches the typical usage checklist). The load limiter was calibrated for the 10t capacity. Safety inspections ensured that the crane stopped correctly at all limits and that emergency stops functioned.
Operational Performance and Benefits
Since commissioning, the 10t LD crane has significantly improved the plant's operations:
- Increased Lifting Capacity: The new crane reliably lifts heavy assemblies up to 10t without strain. Tasks that previously required multiple lifts or forklifts can now be done in a single hoisting move, cutting cycle time. This directly increases throughput on the assembly line.
- Improved Efficiency: Operations like moving machine frames, molds, and equipment parts have become faster. Overhead cranes are known to make assembly and material handling much more efficient. Workers no longer have to reposition loads manually or wait for secondary equipment. For example, the crane now moves heavy mold parts between stations in one lift, which "greatly increases the speed" of the process.
- Enhanced Safety: The risk of manual lifting injuries has dropped. Operators can now lift and transport heavy items safely from the floor to overhead without strain. By mechanizing the lifting, the plant adheres to best practices for industrial safety. In previous systems, manually handling 5+ ton parts exposed staff to pinch and back injuries; the new crane eliminates such direct contact. Features like the overload limiter and limit switches add protection.
- Versatility in Task Handling: The single-girder crane and MD hoist provide smooth control, handling a wide variety of objects. This includes awkward shapes like cast machine frames, large gearboxes, and assembled subsystems. The dual-speed hoist aids in slowly aligning parts during installation, which was hard to do manually. The workshop also uses the crane for routine tasks like lifting tool boxes, maintenance equipment, or even empty pallets. Its flexibility supports almost any heavy lift in the facility.
In sum, the customer reports faster load handling and better workflow. Delays from waiting on heavy lifts have largely disappeared. By having the right crane for the job, the plant avoids overtime and bottlenecks.