- May 19, 2025
- News
Effects of VFD on the Performance of Overhead Cranes
Explore the impact of variable frequency drives (VFDs) on overhead crane performance. Learn how VFD technology can improve efficiency, control, and safety in industrial applications.
A Variable Frequency Drive (VFD) is an electronic motor controller that adjusts an AC motor's speed and torque by varying the supply frequency and voltage. In practice, the VFD converts fixed-frequency AC from the mains into DC via a rectifier, then inverts it back to AC at the desired frequency. By controlling frequency, the drive can make an induction motor run slower or faster (even above its rated speed) to match load requirements. VFDs enable precise speed control and improve efficiency in applications from pumps and fans to lifting equipment.
Key Components and Types
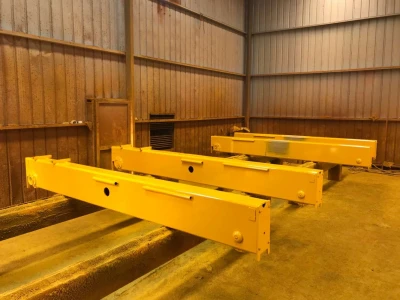

A typical VFD consists of three main power stages and a control unit. These are the rectifier, DC bus/filter, and inverter, plus a control unit (often with scalar or vector control algorithms).
- Rectifier: This first stage uses diodes or thyristors to convert incoming AC to DC. For example, a six-diode bridge (three-phase) or four-diode bridge (single-phase) produces an unfiltered DC waveform. The rectifier's output is a pulsating DC voltage between the positive and negative DC rails, forming the input to the DC bus.
- DC Bus and Filter: The DC bus (sometimes called the DC link) stores and smooths the rectified power. It typically uses large capacitors (and sometimes inductors) to filter out voltage ripples, yielding a stable DC supply. This "smoothing" stage prevents large voltage swings and holds energy between conversion steps.
- Inverter Stage: The inverter (switching section) reconverts the DC into AC at variable frequency. Fast-switching transistors (IGBTs or MOSFETs) chop the DC and create a pulse-width-modulated AC output. By changing the switching pattern, the VFD produces three-phase AC at the desired output frequency and voltage. The inverter stage thus drives the motor with adjustable 3-phase AC, controlling its speed and torque.
- Control Unit (Scalar vs. Vector Control): A microprocessor-based control section manages the VFD's operation. It sets the output frequency/voltage, implements acceleration ramps, and monitors feedback (e.g. motor speed or current). Scalar (V/f) control keeps the voltage-to-frequency ratio constant for simple speed control. Vector (field-oriented) control uses feedback sensors or estimates to independently regulate motor flux and torque, yielding precise dynamic control. In crane hoist drives, vector control is often preferred for tight load regulation and fast torque response. The control unit also provides user interfaces and protective functions (fault detection, overcurrent limits, etc.).
- Braking Units and Resistors (High-Inertia Loads): Overhead cranes have large inertia loads (heavy hooks and loads), so stopping generates regenerative energy. VFDs often include a brake chopper circuit and resistors to handle this energy. When the hoist decelerates, the motor acts as a generator; excess energy is dissipated in braking resistors via the brake chopper to prevent DC bus over-voltage. Alternatively, some high-end systems use regenerative drives (active front ends) that feed energy back to the grid. In practice, many cranes simply use external resistors, since space or cost constraints can limit regenerative setups.
Advantages of Using Variable Frequency Drives
Using VFDs in overhead crane controls offers many benefits:
- Enhanced safety and anti-sway control: VFDs allow smooth acceleration and deceleration, which reduces sudden jerks that can induce crane structure stress or load swing. Many drives include sensorless anti-sway algorithms that automatically stabilize the hoist load. By minimizing swinging loads, VFD-based anti-sway systems let operators drive cranes faster with lower risk. In fact, field reports show overhead cranes with built-in sway control complete operations up to 60% faster than ordinary cranes. This is because operators no longer have to pause for pendulum swings. Overall, VFDs' precise speed regulation and programmable deceleration greatly enhance operating safety and stability.
- Energy savings in bridge cranes: VFDs optimize motor power by matching speed (and therefore torque) to load requirements. Unlike simple on/off starters or two-speed drives, a VFD draws only the current needed for the load. This can lead to large energy reductions, especially in frequent start-stop use. Crane systems often idle or run light loads; at lower speeds the VFD can reduce voltage and frequency so the motor consumes less power. In practice, retrofits with VFD controls have reported substantial savings. In overhead cranes, similar efficiency gains are possible, especially on high-duty-cycle operations. Modern drives also support energy-recovery modes: when lowering loads, some drives can return energy to the DC bus or grid instead of wasting it, further improving efficiency.
- Smooth starting/stopping: VFDs implement soft-start and soft-stop ramps, which gently bring the crane up to speed or slow it to a stop. This avoids mechanical shock to the hoist, trolley, and bridge drive systems. By contrast, contactor-based starts apply full voltage instantly, causing stress on gears, brakes, and the structure. The soft ramps also protect the motor from overload/overvoltage surges and overheating, since current is limited during ramp-up. Over time this reduces wear on mechanical parts (couplings, gearboxes, wheels, runway beams, ropes, etc.) and prolongs motor life.
- Improved positioning accuracy: VFD speed control enables very fine movements. Drives can be programmed with multiple speed settings or very slow jogging speeds. For example, some crane VFD systems allow a 40:1 stepless speed range, so operators can "nudge" the hoist at extremely low speed for precise placement. Smooth motion profiles also cut out vibrations and shocks during lifting or lowering. Instead of a sudden stop at the top or bottom, the drive slows gradually, reducing hook bounce. This higher positioning accuracy is critical when handling delicate or high-value loads. In addition, by preventing load swing, the VFD improves load control, so operators spend less time stabilizing the load and more time moving efficiently.
- Increased productivity: The combined effect of precise speed control, anti-sway, and soft ramps boosts throughput. Less load swing means shorter cycle times, and simultaneous control of bridge, trolley, and hoist motion is possible (e.g. moving diagonally) for faster jobs. In practice, VFD-driven cranes can run multiple motions at once and achieve higher duty cycles, so material handling is smoother and faster than with simple starters.
- Additional smart functions and safety features: Modern VFDs integrate many useful functions beyond basic speed control. Drives can perform dynamic braking (actively slowing the crane), allow hover (holding the load motionless mid-air), and implement "quick-stop" braking if needed. Built-in fault detection and diagnostics let maintenance staff troubleshoot issues quickly. Drives often include programmable limit switches, fault alarms, and status indicators. Critically, safety functions such as Safe Torque Off (STO) are usually built in, ensuring compliance with safety standards. Some drives even feature load drop protection: if a fault or power loss occurs, the drive can engage brakes in a controlled way. By contrast, fixed-speed control has none of these integrated protections. Together, the advanced features of VFDs (overvoltage/undervoltage protection, overcurrent/thermal protection, etc.)add layers of safety for both the equipment and personnel.
Precautions When Applying Frequency Converters to Bridge Cranes
When installing a VFD on a heavy crane, certain precautions are important:
- Match VFD to load and duty cycle: Overhead cranes often fall into CMAA heavy-duty classes (Class D–F) with frequent starts and heavy lifts. The VFD must be sized for the actual motor current and the crane's duty cycle, not just nominal horsepower. For example, specifying a VFD requires data on motor amperage, expected lift weights, and hours of operation. Drives should be rated for high overload capacity to handle the inrush of starting heavy loads. In practice, this means selecting industrial-grade drives (often called "crane grade" or "high-bandwidth" drives) that can withstand rapid reversals and long duty periods. Otherwise, a drive might overheat or trip frequently under high-stress crane duty.
- Include braking units and resistors: As noted, lifting and lowering heavy loads produces regenerative (braking) energy. Without proper equipment, this can over-voltage the drive. Therefore, most crane VFD installations require a brake chopper and an external resistor bank. The resistor (sometimes called a dynamic braking or brake unit) is chosen based on the crane's inertia and duty. It must be sized to absorb the worst-case regenerated energy until it can dissipate. In some systems, multiple braking resistors are switched in for large loads. Alternatively, if space and budget allow, an active front-end (regenerative drive) can be used so that excess energy is returned to the supply grid. Without these brakes or regen units, a heavy-load crane will trigger over-voltage faults whenever a load is rapidly lowered. Regular maintenance of brake resistor fans and checking resistor health is also essential, since a failed resistor can disable braking.
- Use appropriate control modes: For very precise or heavy-lift tasks, consider closed-loop vector control or encoders. Although scalar (open-loop V/Hz) drives are simpler, they have speed/torque limits under heavy inertia. Vector-controlled VFDs (with or without encoder feedback) can hold speed and torque more accurately, which may be necessary for high-precision lifting or tandem hoists. This helps ensure that the crane meets performance requirements without undue overshoot or oscillation. In short, match the drive control strategy to the application: high-inertia, high-precision lifts usually benefit from feedback control.
- Other considerations: VFDs introduce harmonics onto the power line. In large crane installations, it may be necessary to install line filters or an active front end to meet electrical standards. Also, ensure the drive's enclosure and cooling are suitable for crane environments (dirt, dust, outdoor, etc.). Finally, crane operators may need training: VFD controls feel different than simple start/stop controls, and proper setting of ramp times and limit switches is vital for safe operation.
Overall, careful specification and proper auxiliary components (braking, filters, safety relays) are needed to fully realize the benefits of VFD-driven cranes. When correctly applied, variable frequency drives significantly improve the performance, safety, and efficiency of overhead crane systems.